Con la realización de las dos primeras cirugías de alta complejidad que resultaron en el implante de prótesis hechas a medida con tecnología aditiva (impresión 3D en titanio trabecular), realizadas la semana pasada en el servicio de ortopedia y traumatología del Hospital de Clínicas de la Ciudad de Buenos Aires (HCCBA), se dio por inaugurado el primer Laboratorio de tecnologías aditivas aplicadas del país, un ámbito de intercambio de conocimientos, con aplicación e impacto directo en el ámbito médico. El servicio de TyO (traumatología y ortopedia) del HCCBA representado por su Jefe de Servicio, el profesor Marcelo Melo, y PROTOLAB 3D, una división de la firma NOVAX DMA SA, representada porsu presidente, el Dr. Daniel Fiz, decidieron unir sus capacidades, experiencia y conocimientosmédicos, tecnológicos, industriales y sanitarios, para crear el primer Laboratorio de Tecnologías Aditivas Aplicadas(LTAA). “El LTAA es un ámbito de trabajo donde podremos volcar toda nuestra experiencia de 22 años en la industria médica, y más de 10 en el uso cotidiano de las tecnologías aditivas al diseño y desarrollo de implantes a medida, diseñados y fabricados a partir del uso de la impresión 3D o TA, siguiendo los lineamientos médicos de experiencia de los profesionales de este prestigioso centro de salud universitario”. Todo esto ocurre dentro del marco regulatorio de la Administración Nacional de Medicamentos, Alimentos y Tecnología Médica(ANMAT).
Como presidente de NOVAX DMA y médico traumatólogo formado en el HCCBA siento un enorme placer por poder ofrecer al hospital mis conocimientos e infraestructura para realizar implantes específicos que puedan mejorar la calidad de vida de los pacientes. El enorme prestigio de este hospital, resultado de la gran capacidad de los profesionales que lo integran, crea el ámbito ideal para trabajar en esta nueva y revolucionaria tecnología o conjuntos de tecnologías, que, guiadas por el conocimiento médico, están cambiando la manera de dar soluciones a los pacientes.
El LTAA es un ámbito de trabajo donde podremos volcar toda nuestra experiencia de 22 años en la industria médica
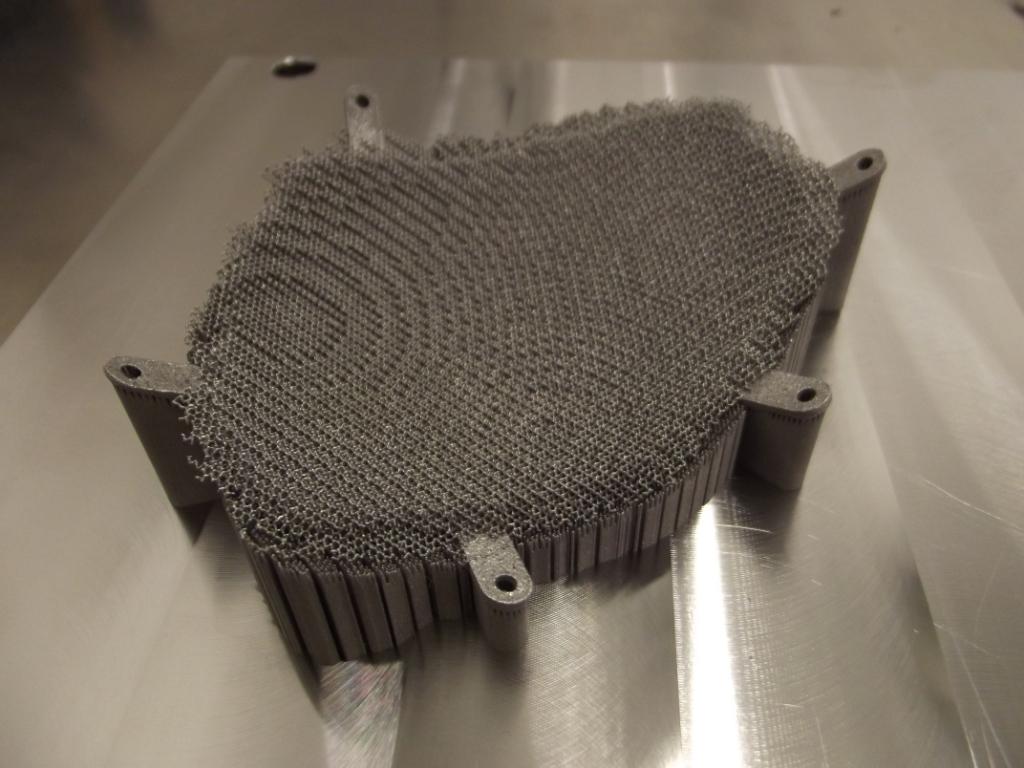
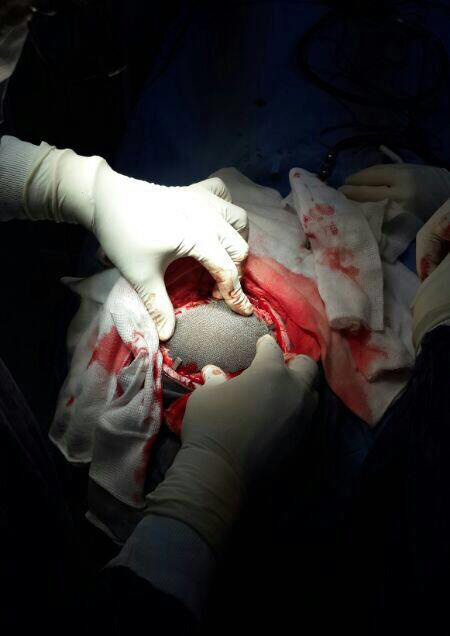
Caso 1
La semana pasada, en este hospital el profesor Marcelo Melo implantó con éxito el primer reemplazo de columna masivo de tres vértebras (L4/5 y S1) diseñado y fabricado íntegramente a partir de polvo de titanio en una impresora 3D, en un paciente joven con un tumor que infiltraba su columna lumbo-sacra.
Para lograr esto, el equipo del LTAA se reunió en múltiples ocasiones, “el primer paso es reconstruir en forma digital y tridimensional las imágenes tomadas al paciente por medio de una Tomografía Axial Computada (TAC). Esto crea un archivo digital tridimensional que podemos mover, examinar e intervenir con herramientas digitales, que nos permiten cortar, suprimir, separar tejidos o agregarle partes o piezas diseñadas en otros software de diseño para posteriormente imprimir en plástico a través de impresoras 3D el modelo de la columna infiltrada por el tumor. Luego, se realiza la extirpación del tumor de forma virtual en la computadora y se imprime el modelo de la columna tal como quedaría luego de la resección del tumor. Finalmente, se diseña el implante que va a reemplazar las vértebras resecadas. Hemos diseñado este implante teniendo en cuenta la anatomía particular del paciente, las dimensiones, las direcciones más adecuadas de los tornillos que lo fijarían al esqueleto, y hasta hemos diseñado los espesores de las paredes para que soporten mejor las exigencias mecánicas , y las textura trabecular similar al hueso en un 100%, para que el implante se pueda fijar biológicamente al hueso del paciente.De esta manera se logra que el implante sea lo más anatómico posible para ese paciente en particular. Luego de validar el modelo del implante diseñado, lo hemos fabricado mediante impresión 3D en titanio. Este es un proceso de alta tecnología en el que un rayo láser derrite las partículas del titanio en polvo capa por capa, generando de esta manera la forma exacta del implante diseñado, todo en una sola pieza, lo que hace posible la generación de geometrías que serían imposibles de hacer mediante técnicas convencionales de fabricación de implantes”. Dr. Daniel Fiz.
[Este proceso…] lo que hace posible la generación de geometrías que serían imposibles de hacer mediante técnicas convencionales de fabricación de implantes”. Dr. Daniel Fiz.
Caso 2
“El mismo proceso se utilizó para planificar, diseñar y fabricar la cirugía de reconstrucción compleja de acetábulo realizada también la semana pasada en el HCCBA por el Dr. Juan Otolengui, quien, con gran destreza, debió retirar del fondo de la pelvis de un paciente una prótesis de cadera que, por el uso, se había hundido generando un enorme defecto en la pelvis del tamaño de una pera grande. “Para resolver este tipo de casos, en la actualidad se utilizan diferentes técnicas de reconstrucción, que incluyen la colocación derodajas de injerto óseo para intentar rellenar esas enormes cavidades con el objetivo porterior de adaptar un implante estándar. Con esta tecnología, o suma de tecnologías, podemos diseñar un implante que se adapte completamente a la forma del defecto que tiene el paciente, rellenándolo en un 100% y creando una estructura trabecular en el implante para que se fije biológicamente al hueso del huésped. La posibilidad de tener los modelos de plástico en las manos antes de la cirugía es de una enorme ayuda para la planificación pre-operatoria. Podemos entender mejor lo que el paciente tiene, planificar mejor, y hasta ejecutar ciertos pasos de la cirugía en el modelo antes de abordar al paciente”.
Antecedentes
Ese mismo día de la semana pasada se realizaba en el Hospital Anchorena una implantación de una porción de maxilar inferior con un implante realizado por Novax con el uso de la misma tecnología hace unos meses atrás, el neurocirujano Raúl Santivañez fue el primero en colocar un implante de cráneo diseñado por Novax dma con la misma tecnología en el Sanatorio de la Trinidad de Quilmes, noticia que recorrió el mundo en los portales especializados de tecnología. (agregar link) Meses atrás, en el Hospital Militar Central de la Ciudad de Buenos Aires, se implantó un reemplazo de 10cm del radio de una paciente con un implante a medida, realizado por Novax con la misma tecnología.
Novax dma no sólo está completamente involucrado en el proceso del diseño y fabricación de implantes a medida en titanio trabecular con tecnología aditiva, sino que en los próximos meses lanzará su línea de implantes estandarizados, fabricados con la misma tecnología, que le otorga al implante características únicas en cuanto a su resistencia mecánica, optimización de la distribución del material y superficie trabecular para su fijación biológica. “Estoy convencido de que con el uso y la aplicación de estas tecnologías, sumadas al enorme conocimiento de los profesionales médicos del HCCBA y otras instituciones, así como la preparación y experienciade los bioingenieros y diseñadores que forman parte del staff de Novax dma podremos dar las mejores y más modernas soluciones a los pacientes, similares a las que hoy día son de punta en los países más avanzados del mundo”. DR. DANIEL FIZ
Estoy convencido de que con el uso y la aplicación de estas tecnologías, sumadas al enorme conocimiento de los profesionales médicos del HCCBA y otras instituciones, así como la preparación y experienciade los bioingenieros y diseñadores que forman parte del staff de Novax dma podremos dar las mejores y más modernas soluciones a los pacientes, similares a las que hoy día son de punta en los países más avanzados del mundo”. Dr. Daniel Fiz